The Ins and Outs of extended Warehouse Management (part 1)
- Canguru
- May 19, 2020
- 4 min read
Updated: Sep 17, 2021

Koen Labie is one of our principal consultants with expertise in the S/4HANA platform of SAP. He has worked on numerous projects with multiple customers and has expanded his knowledge into the Warehouse management package of S/4HANA. We sat together with him to gather the ins and outs of extended warehouse management.
What is the difference between Basic and Extended Warehouse Management?
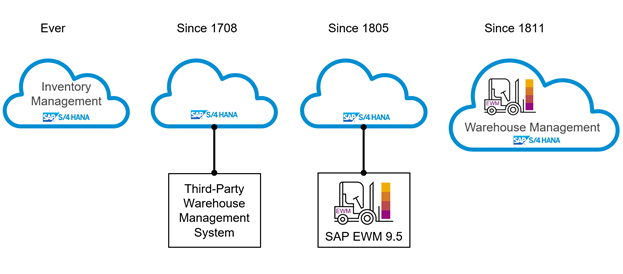
SAP S/4HANA Cloud – Warehousing
Basic warehouse management has grown naturally in most ERP systems together with the need to keep track of a business’ products, their amount and location on site. It allows you to locate your products, and add or remove an amount. Like you would in your backyard shed, keeping track of the amount of screws, planks, and nails you have and where they are located, it is a quite simple structure. In an extended warehouse management, more structure and processes are needed, which results in additional complexity to manage the warehouse. Previously, this was solved by a third party system that was integrated using middleware. Recently, it has been incorporated into the S/4 Hana suite of SAP and no additional integrations are needed.
Is the extended warehouse management a standard product in the S/4 Hana?
Yes, you have a free eWM that exists within the S/4 Hana license. There is also an advanced eWM, which requires additional licenses but has the advantage of more automated processes and therefore increase efficiency in your warehouse.
For example, it sends out a timeslot to each truck that arrives and pre-sends the necessary tasks to the operators to unload the truck within a fixed time. For warehouse employees, this means that no wasted time and that more volume can be processed because of good planning.
Sounds like something every warehouse needs, what are other advantages of this advanced eWM?
The complexity and processes are unique for each business as it is dependent on, for example, the size of your warehouse. However, what all warehouses (or stock rooms) do have in common, is the basic process: products enter the warehouse (packaged or not), receive a number and are placed in a ‘storage location’. With eWM, you can add more steps to this process that are relevant to your specific business.
For example, a truck is provided with a ‘loading bay number’ upfront. The unloaded products will receive an intermediary staging location because you need to decide if the items need to be repacked. With eWM you can add a quality check in between to reject items if they are not compliant with your quality standards. Afterwards the items are assigned a storage location and are placed there by an operator.
The eWM functionalities have been enhanced in the last couple of years (graph below) which allows for additional complexity as stated in the example.

So, this would give the warehouse an efficiency gain?
The efficiency increases, because the distance an operator must ride to place all the items in a single run is done in less time. The items are not grouped per type, which is their primary attribute, but placed on locations that are more logical, for a more efficient process.
For example, when a truck needs to be loaded, all the items will be transported with a minimum amount of movement. If this process is done regularly, these items will be grouped together on the same location. Same principle applies for a production that always needs the same amount of screws, bolts and/or raw materials, as it is more efficient to place the items together. The extended warehouse management helps with these insights and rapidly increases your warehouse efficiency.
The single-run fetching is like shopping in an Ikea warehouse in fact?
Yes, exactly! In an Ikea warehouse at the end of the showroom there is a large warehouse. There you will take all necessary components of your PAX-cabinet. Most of the times these locations, of the shelves, handles and frame, are scattered throughout the warehouse. Lucky for you, a kiosk is available and will help you by telling you the exact row and shelve number of each of the cabinet parts. The locations usually don’t make sense for you as a end-customer but these are determined by the warehouse management system based on the offloading of the truck. To do this efficiently, all content goes into the same row, no matter if these parts are related or not.

Which companies benefit from the eWM?
All companies with a warehouse and operators who take out items piece per piece. A small growing business will come to a point where their warehouse is managed on the gut feeling of the employees. They will place items on free locations or wherever it makes sense to them. This will continue until the warehouse is a mess and the warehouse responsible cleans the warehouse and moves everything around, again according to their personal ‘logical’ system. The businesses without any agreed warehouse logic but also large production, logistics and retail corporations can benefit from this solution. Again, benefiting means everything is maintained and monitored in one system.
Stay tuned for our second part of the blogpost where Koen will explain how to set up your Extended Warehouse Management (eWM) and what the challenges are.
Comentários